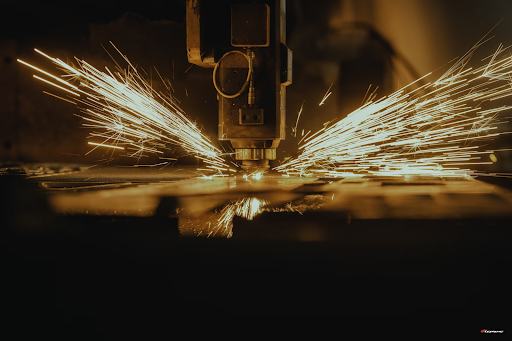
In the world of CNC machining, precision is paramount. Tool eyes, also known as tool setters, tool presetters, or touch sensors, play a crucial role in ensuring that your CNC machine tools are accurately positioned, helping to maintain the highest levels of precision and efficiency. For machinists and manufacturers, choosing the right tool eye is a significant decision that can impact both the quality of the final product and the overall efficiency of the machining process. Among the leading suppliers in this niche are Tooleye and Metrol, each offering unique products designed to meet the specific needs of various CNC machines.
In this blog, we will provide an in-depth comparison between Tooleye and Metrol CNC tool eyes, focusing on their features, cost-effectiveness, and compatibility. By the end of this guide, you’ll have a clearer understanding of which brand might be the best fit for your CNC machining needs.
A Brief Introduction to Tooleye
Tooleye has been a leading supplier of CNC tool eyes, particularly for Mazak machines, since 1995. Over the years, Tooleye has built a reputation for delivering high-quality, reliable tool eyes designed specifically for the demanding environments of CNC machining. One of the key strengths of Tooleye is its focus on compatibility and durability, ensuring that their products not only fit perfectly into Mazak machines but also perform as effectively as the original equipment.
Tooleye offers two main variations of tool eyes for Mazak machines: one with a round mounting flange and the other with a square mounting flange. This simple distinction ensures that machinists can easily select the correct model for their specific needs without worrying about compatibility issues. Moreover, Tooleye’s tool eyes are built with stainless steel construction, carbide touch-off materials, and are designed to be coolant-resistant, making them a reliable choice in harsh machining environments.
Understanding Metrol Tool Eyes
Metrol, another well-known name in the CNC machining industry, also offers a range of tool eyes designed for various CNC machines. Like Tooleye, Metrol provides a variety of models tailored to different machine types, ensuring that customers can find a product that fits their specific equipment. Metrol’s tool eyes are known for their precision and reliability, making them a popular choice among machinists who prioritize accuracy.
However, Metrol’s products tend to be more expensive than Tooleye’s, which can be a significant consideration for budget-conscious buyers. Additionally, Metrol offers different probe models for different machines, but the mounting flange and bolt pattern options are limited, which may lead to compatibility issues if not carefully considered.
Feature Comparison: Tooleye vs. Metrol
When comparing Tooleye and Metrol tool eyes, it’s essential to look at the key features that matter most to machinists: construction quality, compatibility, ease of installation, and cost.
1. Construction Quality
- Tooleye: Tooleye tool eyes are constructed from stainless steel, offering robust protection against corrosion and wear. The touch-off material is made from carbide, which is known for its durability and resistance to breaking, unlike ceramic alternatives. This construction ensures that Tooleye’s products can withstand the rigors of CNC machining environments, reducing the need for frequent replacements.
- Metrol: Metrol tool eyes are also well-constructed, typically using high-quality materials that ensure long-lasting performance. However, some users have noted that certain Metrol models may be more prone to damage under heavy use, particularly if not handled carefully.
2. Compatibility
- Tooleye: Tooleye specializes in CNC tool eyes for Mazak machines, offering two variations: one with a round mounting flange and the other with a square mounting flange. This focused approach ensures that machinists can easily find the correct model for their specific machine, with no need for extensive modifications or adjustments. Tooleye also offers models compatible with other brands like Mori Seiki, Okuma, Doosan, and Samsung, particularly those with FANUC controllers.
- Metrol: Metrol offers a broader range of models designed for various CNC machines. While this variety can be advantageous, it also means that users need to be more careful when selecting the correct model to ensure compatibility with their specific equipment. The mounting flange and bolt pattern options are limited, which could lead to issues during installation if not correctly matched to the machine.
3. Ease of Installation
- Tooleye: Tooleye tool eyes are designed for straightforward installation, with clear guidelines provided to ensure that users can quickly and efficiently mount the tool eye onto their CNC machine. The design of the mounting flange, whether round or square, is tailored to fit specific Mazak machines, minimizing the risk of installation errors.
- Metrol: Metrol tool eyes are also relatively easy to install, provided that the correct model is selected for the specific machine. However, due to the variety of models available, users need to be more diligent in ensuring that they have chosen the right product for their needs.
4. Cost
- Tooleye: One of the most significant advantages of Tooleye tool eyes is their affordability. Priced at $495 plus shipping (or $520 plus shipping for the 5-wire unit), Tooleye offers a cost-effective solution without compromising on quality. Additionally, Tooleye products are rebuildable, allowing users to extend the lifespan of their tool eyes and save money in the long run.
- Metrol: Metrol tool eyes tend to be more expensive, which can be a deterrent for some buyers. While they offer high-quality products, the higher price point may not always be justified, especially when comparable alternatives like Tooleye are available at a lower cost.
Performance in Real-World Applications
To provide a better understanding of how Tooleye and Metrol tool eyes perform in real-world applications, let’s look at some common scenarios where these products are used.
Scenario 1: High-Volume Production
In high-volume production environments, CNC machines are often running continuously, with little downtime between jobs. In such settings, the durability and reliability of the tool eye are critical. Tooleye’s stainless steel construction and carbide touch-off material make it an excellent choice for these demanding conditions, as it can withstand the wear and tear of constant use.
Metrol tool eyes also perform well in high-volume production, but the higher cost may be a consideration for businesses looking to maximize their return on investment.
Scenario 2: Precision Machining
For precision machining tasks, where accuracy is paramount, both Tooleye and Metrol offer reliable solutions. However, Tooleye’s compatibility with specific Mazak machines gives it an edge in scenarios where exact fitment is crucial. The ease of installation and the fact that Tooleye products are designed specifically for Mazak machines ensure that the tool eye will work seamlessly with the machine’s existing systems.
Scenario 3: Budget-Conscious Operations
For operations where cost is a significant factor, Tooleye’s affordability makes it the clear winner. The lower price point, combined with the product’s durability and rebuildable design, offers excellent value for money. Businesses that need to outfit multiple CNC machines with tool eyes will find Tooleye’s pricing particularly attractive.
Customer Support and After-Sales Service
Both Tooleye and Metrol offer customer support and after-sales service, but there are differences in the level of support provided.
- Tooleye: Tooleye prides itself on offering exceptional customer support, with knowledgeable staff available to assist customers in selecting the right model for their needs. They also offer same-day shipping for orders placed by 4:30pm CST Monday thru Friday, ensuring that customers receive their products quickly. The rebuildable design of Tooleye tool eyes further enhances the after-sales experience, as users can easily refurbish their tool eyes rather than replacing them entirely.
- Metrol: Metrol also provides good customer support, though their broader range of products can sometimes make it more challenging for customers to find the right model. While their products are reliable, the lack of a rebuildable option means that users may need to replace the tool eye more frequently, which could increase long-term costs.
Final Verdict: Tooleye vs. Metrol
When choosing between Tooleye and Metrol for your CNC tool eye needs, several factors come into play. If you’re looking for a cost-effective solution that doesn’t compromise on quality, Tooleye is an excellent choice. With a focus on compatibility, durability, and affordability, Tooleye offers a reliable alternative to more expensive brands like Metrol.
Metrol, on the other hand, is a solid option for those who prioritize precision and are willing to pay a premium for it. However, for most users, especially those using Mazak machines, Tooleye’s specialized designs and competitive pricing make it the better choice.
In conclusion, Tooleye stands out as the affordable, reliable, and customer-focused option for CNC tool eyes. Whether you’re running a high-volume production line, engaging in precision machining, or operating on a tight budget, Tooleye offers the performance and value you need to keep your CNC machines running smoothly.