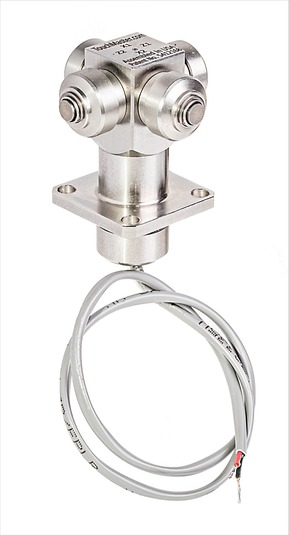
Precision is paramount in CNC machining, and having the right tool presetters is essential. Tool Eye’s CNC tool presetters are designed to maximize accuracy and efficiency in your machining processes. This blog will explore the importance of tool presetters and how Tool Eye’s products stand out in the market.
Precision is paramount in CNC machining. It determines the quality of the final product and the efficiency of the machining process. One critical factor that contributes to precision is the accuracy of the cutting tools. This is where tool presetters come into play.
Tool presetters are devices used to accurately measure and set the cutting tools’ length, diameter, and other critical dimensions. By using a tool presetter, manufacturers can ensure that their tools are set to the correct specifications, reducing the risk of errors and scrap.
Tool Eye’s CNC tool presetters are a valuable asset to any machine shop looking to achieve the highest levels of precision and efficiency. With their advanced technology, user-friendly interface, and robust construction, Tool Eye’s tool presetters are the ideal choice for manufacturers who demand the best.
What Are CNC Tool Presetters?
CNC tool presetters are devices used to measure and set the precise length and diameter of cutting tools before they are used in machining. This ensures that each tool is accurately calibrated, leading to more precise cuts and improved product quality.
CNC tool presetters play a crucial role in the efficiency and accuracy of modern machining operations. These innovative devices are designed to precisely measure and set the length and diameter of cutting tools before they are mounted on CNC machines. By accurately calibrating each tool, CNC tool presetters ensure that machining processes deliver consistent and high-quality results.
The process of tool presetting typically begins when an operator places the cutting tool into the CNC tool presetter. The device then utilizes advanced sensors and measurement systems to gather precise data about the tool’s dimensions. This data is then analyzed by the presetter’s software, which calculates the exact length and diameter of the tool. In some cases, the presetter may also measure additional parameters such as the tool’s runout and eccentricity.
Once the measurements are complete, the CNC tool presetter automatically adjusts the tool’s length and diameter to match the desired specifications. This is achieved through the use of mechanical actuators or servo motors that physically reposition the tool’s cutting edge. The presetter also stores the tool’s calibrated data in its memory, ensuring that the tool can be quickly and easily recalled for future use.
The benefits of using CNC tool presetters are numerous. Firstly, they significantly reduce setup time by eliminating the need for manual tool measurement and adjustment on the machine. This can save a considerable amount of time, especially in high-volume production environments. Secondly, CNC tool presetters enhance machining accuracy by ensuring that each tool is precisely calibrated, leading to more consistent and repeatable cuts. This results in improved product quality and reduced scrap rates.
Furthermore, CNC tool presetters help to extend tool life by minimizing wear and tear on the cutting edges. By accurately setting the tool’s length and diameter, the presetter prevents excessive force from being applied to the tool during machining. This reduces the risk of premature tool failure and ensures that tools can be used for longer periods of time.
Benefits of Tool Eye’s CNC Tool Presetters
- High Precision: Tool Eye’s tool presetters provide highly accurate measurements, ensuring that each tool is perfectly calibrated for the job. This precision leads to better machining outcomes and tighter tolerances.
- Durable Construction: Made with robust materials, Tool Eye’s tool presetters are built to withstand the demands of a busy machining environment. Their durability ensures long-lasting performance and reliability.
- Cost-Effective: Tool Eye offers high-quality tool presetters at competitive prices. This affordability allows businesses to equip their machines with top-notch presetters without breaking the bank.
- Ease of Use: Tool Eye’s tool presetters are designed for easy setup and use, minimizing downtime and training requirements. Their user-friendly interface makes it simple to achieve accurate measurements quickly.
- Rebuildable Design: Like other Tool Eye products, the tool presetters are rebuildable. This feature allows you to repair and reuse them, reducing the need for frequent replacements and lowering long-term costs.
How Tool Eye’s Tool Presetters Enhance Machining
- Improved Accuracy: By ensuring that each tool is accurately measured and set, Tool Eye’s presetters enhance the overall precision of your machining operations. This accuracy leads to better product quality and fewer errors.
- Increased Efficiency: Accurate tool presetting reduces setup times and minimizes the need for manual adjustments during machining. This increased efficiency translates to higher productivity and lower operational costs.
- Reduced Waste: Precise tool presetting helps reduce material waste by ensuring that each cut is accurate and consistent. This not only saves money but also supports sustainable manufacturing practices.
- Enhanced Safety: Properly set tools reduce the risk of accidents and equipment damage. Tool Eye’s presetters help maintain a safer work environment by ensuring that all tools are correctly calibrated.
- Flexibility: Tool Eye’s tool presetters are compatible with various CNC machines, providing flexibility to use them across different applications and projects.
Indispensable Tools for Modern Machining
CNC tool presetters are indispensable tools in modern machining operations. Their ability to precisely measure and set cutting tools helps to streamline production processes, improve accuracy, enhance product quality, and extend tool life. By investing in a CNC tool presetter, manufacturers can gain a competitive advantage by increasing their efficiency, reducing costs, and delivering superior-quality products to their customers.
Tool Eye’s CNC tool presetters are essential for maximizing precision and efficiency in your machining operations. With their high accuracy, durable construction, cost-effectiveness