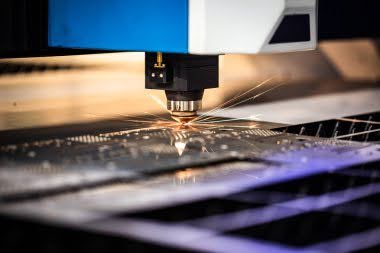
In the fast-evolving world of CNC machining, accuracy and efficiency are critical to success. As the demands of precision manufacturing continue to grow, so does the need for cutting-edge tools that can keep up with these challenges. Tooleye’s innovative tool setter solutions represent the future of CNC machining, offering advanced technology that improves accuracy, reduces downtime, and enhances the overall efficiency of manufacturing operations.
Since 1995, Tooleye has been a leader in producing high-quality CNC tool setters for Mazak and other leading CNC machine brands. Known for their durability, rebuildable design, and precision, Tooleye’s tool setters are paving the way for the next generation of CNC machining solutions.
The Role of Tool Setters in CNC Machining
Tool setters, also known as tool presetters or touch sensors, play an essential role in CNC machining by ensuring that cutting tools are accurately measured and calibrated before machining begins. They measure the length and diameter of the tool and provide real-time data to the CNC machine, which then adjusts its toolpath accordingly.
This process eliminates the need for manual measurement, significantly reducing the risk of human error and ensuring that each part is machined to exact specifications. Accurate tool measurement is crucial for avoiding costly mistakes, improving efficiency, and maintaining high product quality.
Tooleye’s Innovative Approach to Tool Setting
Tooleye’s tool setters are designed with innovation at the forefront. Here’s how their solutions are shaping the future of CNC machining:
1. Precision Measurement for High-Tolerance Parts
Tooleye’s tool setters offer precision measurement that ensures cutting tools are positioned with absolute accuracy. This is especially important when machining high-tolerance parts, where even the smallest deviations can lead to defects or non-compliance with industry standards. By providing real-time, highly accurate tool measurements, Tooleye’s solutions improve overall part quality and reduce rework.
2. Enhanced Durability for Long-Term Use
Unlike many competitors, Tooleye’s tool setters are built to last. Their stainless steel construction and carbide touch-off components ensure that the tool setters can withstand the harsh conditions of a CNC machining environment. This enhanced durability minimizes downtime caused by sensor failures and extends the lifespan of the tool setters, making them a more cost-effective solution in the long run.
3. Rebuildable Design for Sustainability
As industries move towards more sustainable practices, the rebuildable design of Tooleye’s tool setters is a major advantage. Instead of discarding worn or damaged sensors, manufacturers can rebuild Tooleye’s tool setters at a fraction of the cost of buying new ones. This not only saves money but also reduces waste, contributing to more environmentally friendly manufacturing operations.
The Future of CNC Machining: Automation and Efficiency
Tooleye’s tool setters are a prime example of how automation is driving the future of CNC machining. Manual tool measurement and calibration are time-consuming processes that are prone to human error. By automating these tasks, Tooleye’s tool setters significantly reduce setup time and improve the accuracy of each part produced.
Automation is becoming increasingly important in the manufacturing industry as companies strive to increase productivity while maintaining quality. Tooleye’s solutions align with these goals by providing the automation needed to streamline operations and meet the demands of modern manufacturing.
Adapting to Industry 4.0
As CNC machining continues to evolve, the integration of digital technologies and data-driven processes—often referred to as Industry 4.0—is transforming the way manufacturers operate. Tooleye’s tool setters are equipped to meet the demands of Industry 4.0 by providing real-time data that can be used to optimize machining processes.
With Tooleye’s innovative tool setter solutions, manufacturers can gain valuable insights into tool wear, machine performance, and production efficiency. This data can be used to make informed decisions, reduce downtime, and improve overall operational efficiency.
Why Tooleye Leads the Way in CNC Tool Setting
Tooleye’s commitment to innovation, precision, and durability has made them a leader in CNC tool setting solutions. Here’s why Tooleye continues to lead the way in shaping the future of CNC machining:
- Proven Expertise: Tooleye has been a trusted supplier of tool setters for Mazak and other leading CNC machine brands since 1995. Their decades of experience in the industry ensure that their products meet the highest standards of quality and performance.
- Cutting-Edge Technology: Tooleye’s tool setters incorporate the latest technology to provide precise, real-time measurements that improve machining accuracy and reduce errors.
- Sustainable Solutions: The rebuildable design of Tooleye’s tool setters offers long-term cost savings while supporting sustainable manufacturing practices.
The Future is Bright with Tooleye
As CNC machining continues to evolve, the need for innovative, reliable, and precise tool setting solutions is more important than ever. Tooleye’s tool setters are at the forefront of this evolution, offering cutting-edge technology that enhances accuracy, reduces downtime, and supports the demands of modern manufacturing.
Whether you’re looking to improve machining efficiency, reduce waste, or gain valuable insights into your production processes, Tooleye’s tool setter solutions are the key to staying competitive in the future of CNC machining.